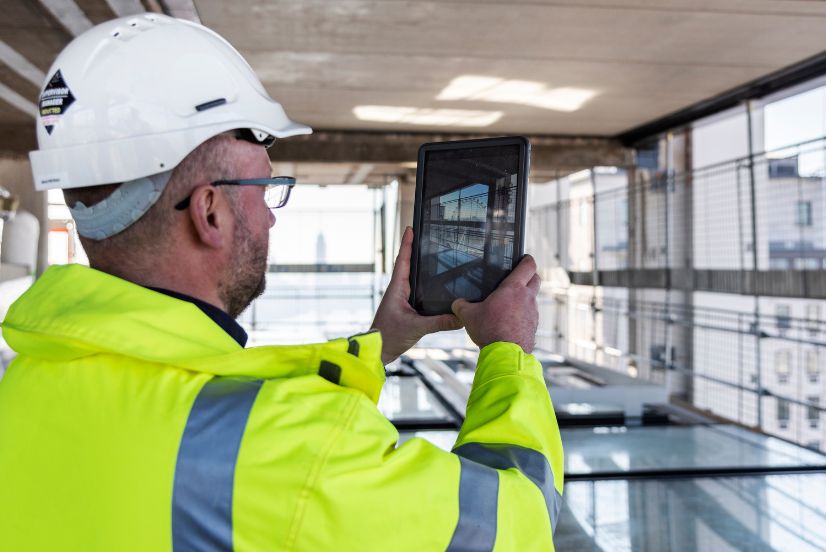
What is construction rework, and why is it relevant for the Singapore construction industry in 2024?
Construction rework occurs when corrective actions or modifications are necessary for a construction project. For the Singapore construction industry, construction rework remains significant for several reasons:- Cost Implications: Rework often results in additional costs for materials, labor, and time. Managing and minimizing rework is crucial for controlling project budgets and ensuring profitability for construction firms.
- Project Delays: Rework can lead to project delays, impacting the overall schedule and potentially causing financial penalties for missing deadlines. Timely project completion is crucial for meeting contractual obligations and client expectations.
- Quality Assurance: Singapore has stringent national building codes and standards, to ensure the safety and quality of constructed buildings. Rework may be necessary to bring a project in compliance with these standards, and ensuring quality is essential to avoid legal issues and reputational damage.
- Sustainability and Environmental Concerns: Construction rework often generates additional waste and has environmental implications. Minimizing rework aligns with sustainability goals and regulations, promoting environmentally responsible construction practices.
- Technology Integration: In 2024, the Singapore construction industry may see increased integration of technology, such as Building Information Modeling (BIM) and advanced project management software. These tools can help detect and resolve issues early in the design and construction phases, reducing the likelihood of rework.
- Client Satisfaction: Meeting client expectations is crucial for the success of construction projects. Rework can lead to dissatisfaction and strained client-contractor relationships. Minimizing rework helps ensure that the final product aligns with the client’s vision and requirements.
- Industry Competitiveness: Construction firms that effectively manage rework are likely to be more competitive in the industry. Efficient project delivery, adherence to quality standards, and cost control contribute to a construction company’s reputation and competitiveness.
More than profit margins: The cost of construction rework
According to a study conducted by the Construction Industry Institute (CII), rework accounts for an average of 9% of construction costs and causes project delays of approximately 18% on average. Rework can also diminish labour productivity by up to 20%, leading to longer project durations and increased costs. When it comes to construction rework, the costs incurred can extend far beyond mere inconvenience on site. The financial implications of rework for any company can be substantial, with expenses adding up quickly. Any construction defect resolution, whether it involves structural adjustments, system modifications, or cosmetic revisions, brings additional labour, material, and equipment costs. These expenditures often catch project budgets off guard, eating into profit margins that could have been otherwise preserved.Identifying the root causes of construction rework
To effectively address and prevent construction rework, it’s crucial to understand the underlying causes. Rework can arise from various issues, such as design flaws, material defects, miscommunication, and inadequate quality control. For example, a flawed project design may require structural alterations, leading to costly delays. Similarly, substandard materials might necessitate system modifications and corrective actions. Miscommunication between project stakeholders can also result in misunderstandings, requiring cosmetic or structural changes to successfully resolve the issue and ensure the build meets regulatory specifications. Imagine a construction project where design issues come up during construction, requiring frequent and time-consuming adjustments. This not only adds significant material and labour costs but also causes delays, affecting project completion and pushing back the build timeline. Similarly, consider situations where poor quality control leads to material defects that need repairs. These instances emphasize the need to address the root causes of construction defects. Conducting thorough root cause analysis is essential to effectively tackle construction defects – so, understanding why rework happens is the first step towards implementing efficient construction defect prevention and management strategies.Best site practices for construction rework prevention
- Effective Planning and Design: Before construction commences, thorough planning and meticulous design are essential. This includes comprehensive project specifications, architectural drawings, and engineering plans that leave no room for ambiguity. For example, a well-planned project might involve detailed structural project plans, specifying the exact type and placement of steel beams to avoid potential rework.
- Quality Control and Inspections: Quality control measures are instrumental in preventing rework. Regular inspections should be conducted at critical project milestones to identify and address any deviations from the design or quality standards. For instance, concrete strength tests can be performed during foundation pouring to ensure compliance with structural requirements.
- Communication and Collaboration: Effective communication and collaboration among project stakeholders are crucial. This includes clear and open lines of communication between architects, engineers, contractors, and subcontractors. An example of this could be having regular meetings to discuss any design or construction concerns and to ensure that everyone is on the same page regarding project expectations.
- Technology and Tools: Modern technology and tools offer construction professionals advanced ways to prevent rework. Building Information Modelling (BIM) software, for instance, allows for 3D modelling and virtual simulations to identify potential clashes or issues in the design phase. This proactive approach minimizes defects caused by design conflicts discovered during construction.