The construction industry has the second-highest rate of fatalities across all industries in the UK according to the Health and Safety Executive (HSE) website statistics for 2019. Sadly, 30 people lost their lives during 2019 due to incidents on the construction site. With another 54,000 non-fatal injuries reported across the year, there is clearly a way to go when managing health and safety in construction to prevent further deaths and long-term conditions.
The construction industry is the European Union’s (EU) largest industry employer. A workforce of 18 million contributes to 9% of the EU’s gross domestic profit (GDP). This large and diverse workforce provides an invaluable service to society and the prosperity of each nation. So, why are there still so many incidents on construction sites and how can health and safety regulations work to protect our workers?
Targeting the big five
Five main categories of incidents are most common on construction sites:
- Falls from height – which account for 49% of fatalities and 18% of non-fatal injuries (a number that is 10% higher than the statistics for all other industries)
- Slips, trips or falls on the same level – accounting for 25% of non-fatal injuries
- Being trapped by something collapsing or overturning – responsible for 14% of fatalities
- Being struck by a moving, falling or flying object – the cause of 10% of fatalities and 12% of non-fatal injuries
- Injured while handling, lifting or carrying – making up 20% of non-fatal injuries
Besides these main issues, construction workers are at an increased risk from other serious and life-changing conditions. Conditions such as chronic obstructive pulmonary disease (COPD), occupational deafness, hand-arm vibration syndrome (HAVS) and asbestosis are serious and life-altering conditions that can be caused, or aggravated, by conditions on-site.
Health and safety legislation should be at the core of all construction businesses and every project, it should be a top priority for senior managers and it should be embedded into every plan, decision and activity. Read on for ideas on how to manage health and safety in construction, to ensure that your staff are safe, give confidence to your clients, maintain a flawless health and safety record and save time and money through introducing safety measures.
Assess and avoid
Risk assessments should be the first stage of all construction projects. Health and Safety teams should be involved in early planning to ensure that the health of workers is embedded in the project.
Avoidance is the first key step. Is an activity deemed as dangerous? Can it be carried out in an alternative way that would avoid the danger? Can working at height be removed altogether or can fabrication be carried out on the ground and the structure lifted to height for fixing? Are hazardous chemicals essential to work, or can alternatives be found?
If time constraints or pressure from third parties will impact on the health and safety of your staff, these issues should be flagged to all stakeholders. If the risk can’t be removed, then safe working conditions should be made available through the correct equipment or protocols. If the situation can’t be made safe, then the group must work to change the working parameters. Time or client pressures should never impact the safety of workers on site. No project is that important.
Health & Safety: Do you have the skills on-site?
Once all stakeholders have understood and accepted the risk parameters for a project, plans must be put in place to reduce these risks. The main aim, and the measure of success for all health and safety teams, is for a project to run with zero reported incidents.
Checking the qualifications and experience of all workers and supervisors is key. Workers must be able to perform tasks confidently and competently to reduce the risk to themselves and others. Construction Skills Certification Scheme (CSCS) card checks are a must in the UK and a full log of each card, every contractor and their competency to carry out a task must be documented. Where gaps in knowledge or experience are identified, training should be provided or new staff must be brought in to complete the task. If this can’t be done, then the task must be changed to accommodate the experience of the workers on-site, even if this does add extra time or cost.
Ensure that qualified Health, Safety and Environment (HSE) officers are known to all workers and that all staff know how and when to report a dangerous situation. Whether you have a dedicated HSE officer on-site, site office staff logging incidents or an app-based solution everyone can access, it should be easy for anyone to report an incident.
Make protective equipment a habit
Once you have the right workers with the correct experience, they must have access to the correct personal protective equipment (PPE) to carry out the job safely. Every person on site should understand the risks to themselves and those around them and know which equipment they need to complete the task safely. Wearing the necessary equipment should become second nature and this only happens if everyone adheres to the rules, if the equipment is missing, there should be a quick and easy way for staff to request it.
Managers should model the behaviours expected of their teams. Everyone should be free to stop work and demand equipment if it is not available and to request that others in their team do the same.
Health and safety regulations become a habit when the culture enables team members to express their views openly. This open and honest approach rewards workers who show behaviours that protect their own safety and those of their colleagues.
The right tools for the job
This theme carries through to the suitability of equipment too. All equipment, from pneumatic drills and saws to large earthmoving machinery, should be assessed for its suitability and safety. Does the equipment pose a risk to the worker? Can a different piece of equipment give the same result with lower risk? If we do have to accept a risk, does the equipment minimise the risk in the best way? What other checks do we need to ensure zero incidents whilst using this equipment?
Checks don’t stop when the equipment is in use. Maintenance schedules are essential to ensuring the safety of equipment and safeguarding those using it. A robust service and maintenance routine should be developed, assigned to an individual or team and monitored throughout the project, with any checks or maintenance work documented.
Identify issues, make changes and demonstrate the impact
Software really can be a health and safety professional’s best friend. A good software package will allow easy data collection from multiple team members in multiple locations. Everyone should be able to easily report a health and safety concern, record standard health and safety data and complete assessments. The best software allows for collection through app-based systems, enabling any smartphone to become a data collection device.
Once data is recorded, software should help you to easily identify hazards and other issues, show where changes were made, demonstrate the impact of these changes and allow for easy reporting to senior management. This comprehensive and closed-loop data flow is essential for demonstrating regulatory compliance and for providing evidence during inspections.
By moving to a continuous improvement culture, issues that are flagged and dealt with on one project can be carried through as health and safety requirements for the next project. This process ensures that the same problem isn’t repeated and that everyone learns from previous mistakes.
The PlanRadar app is the perfect tool for completing comprehensive digital health and safety assessments through straightforward templates. Fire assessments and other specific templates can be designed, saved and adapted for future projects. And, most importantly, where plants require no transmitting appliances, PlanRadar can be used in an offline mode, automatically syncing information as soon as the device is reconnected to a network. This functionality can be essential to COSHH assessments.
Work hard, but rest hard too
When time pressures are mounting and the threat of late fines are looming, it’s tempting to cut corners and push to get a project done, but this should never be at the expense of health and safety. If changing plans impact on people, equipment or procedures, then risk assessments should be re-evaluated.
Although contractors should expect high standards of work and output from their workers, rest is important too. Workers need to be highly alert to their surroundings and to help keep everyone safe; this is especially important when working at height, with hazardous material or in confined spaces. Workers should be given adequate time to rest and relax and not be pushed to work overly long hours, even if they request the overtime. Distraction and tiredness lead to mistakes and they can be serious and even life-threatening.
If in doubt, shout
Businesses that excel at managing health and safety in construction have safety at the very core of their work and everyone on-site sees the benefit of the precautions, follows the rules and enforces them within their teams.
Communication is key here. When an individual understands why a rule is in place or why something has changed, they are more likely to comply and enforce compliance from others. When you have zero incidents during a project, reward the team for achieving this. If a near-miss has occurred, communicate this to the team, help them to understand why it happened and how further incidents can be avoided. Be clear about the changes you’ve made to make ensure the incident doesn’t occur again and how others can contribute to this adjustment.
Health and safety in the construction industry is the responsibility of everyone on site. Put simple procedures in place so that construction workers can quickly and easily report an issue and instil a culture of responsibility. If a trip hazard is identified, encourage workers to remove it. If someone is in danger, encourage others to act. Dealing with an issue when it arises can help reduce immediate incidents that may follow.
Health and safety rules should be repeated at daily briefings and reinforced throughout the day. There are many ways to remind workers of their health and safety obligations, perhaps through posters displayed around the site or reminders on software tools.
Several of the bigger construction companies have powerful slogans to help educate and engage all team members on-site.
Balfour Beatty’s award-winning golden rules highlight core expectations and they are simple and easy to remember:
Meanwhile, Amey’s Target Zero encourages workers to speak out and talk about health and safety issues so that problems can be identified and dealt with quickly.
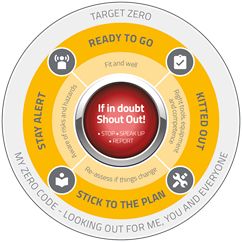
Amey’s Code Zero training aims to bring their Lost Time Injury Incident Rate to zero by 2021.
We have all the tools to achieve zero incidents and to make the construction site a safe place for all workers. By taking a thorough approach to identifying risk, developing a culture of open and honest communication and ensuring workers have access to the safest tools for the job, we can reduce injuries on-site and achieve zero incidents.