Improving quality in your construction projects doesn’t mean you have to turn everything upside down. In fact, and as hard as it may be to believe, just following a few simple steps can make a big difference, no matter how big or complicated the project is.
People pick construction companies they trust, and that trust comes from a reputation for quality. Delivering shoddy work erodes that trust while exceeding expectations.
Contents:
1. Implement regular training programs
2. Conduct regular quality inspections
3. Foster a culture of quality
4. Effective planning and scheduling
5. Use construction management software like PlanRadar
This article is going to show you some straightforward but effective ways to up your game in construction projects. This means happier clients, a happier workforce, and a name that’s known for being trustworthy.
These steps are broken down into sections, which you can jump to using the following contents:
- Implement regular training programs
- Conduct regular quality inspections
- Foster a culture of quality
- Effective planning and scheduling
- Adopt construction management software like PlanRadar
Before we get into it, if you’d like to quickly see how PlanRadar can improve the quality of your construction projects, this video is a great introduction.
Want to find out what PlanRadar can do for your quality assurance? Book a demo with the team today.
Implement regular training programs
Investing in your team’s development sends a powerful message: you value their growth and success. It fosters a sense of confidence and ownership, motivating workers to take pride in their work and strive for excellence.
What’s more, a well-trained workforce is more engaged and collaborative, leading to better communication and problem-solving on-site.
Like any high-performing team, a construction project’s success hinges on its members’ knowledge and expertise. The training sessions hone your team’s skills in crucial areas like:
- Quality control procedures: Giving your workers the expertise to spot and fix problems early on can save you from expensive do-overs and delays.
- Safety protocols: A trained workforce understands and adheres to safety regulations, minimizing accidents and injuries.
- New technologies and tools: Staying ahead of the curve with the latest advancements in construction technology leads to more efficient and effective work.
Training is not a one-time event; it’s an ongoing process. Consider a variety of formats to cater to different learning styles and preferences, including:
- Interactive workshops that cover specific topics in detail.
- On-the-job training where experienced mentors guide and coach workers in real-time situations.
- Online resources, such as e-learning modules and video tutorials, offer flexibility and accessibility.
Conduct regular quality inspections
A minor crack in the foundation today could become a structural nightmare tomorrow. Regular inspections catch these early-stage issues before they snowball into major repairs and delays. Addressing minor issues during construction is far cheaper than fixing major defects after completion.
Regular, thorough inspections demonstrate your commitment to quality. They build trust with clients, partners, and investors, enhancing your reputation as a reliable and responsible builder.
Inspections aren’t one-size-fits-all. Use clear checklists, document findings thoroughly, and take prompt corrective action to address identified issues. Tailor your approach to each stage of the project:
- Pre-construction: Verify the compliance of permits, materials, and equipment before the first brick is laid.
- During construction: Regularly check workmanship, materials, and adherence to safety protocols.
- Final inspections: Ensure the completed project meets all specifications and standards before handover.
Make inspections a priority, schedule them regularly, involve your team, and use the findings to improve continuously.
Foster a culture of quality
A culture of quality means every worker takes ownership of their work. They don’t just follow instructions; they understand the bigger picture and strive for excellence in every detail. It takes consistent effort, open communication, and a genuine commitment from everyone involved.
Here’s how you can foster this culture:
- Start with “why”: Help your team understand the purpose of the project. Connecting individuals to the impact of their work breeds passion and commitment.
- Empower, don’t dictate: Trust your team’s expertise. Make them problem-solvers, not just task-doers. Provide clear goals and boundaries, but give them the freedom to find the best way to achieve them to build confidence and ownership.
- Catch them doing it right: Don’t just point out mistakes; recognise and celebrate good work. A simple “thank you” or a public shout-out can go a long way in motivating people to take pride in their craft.
- Make quality visible: Track progress, share inspection results, and showcase success stories. Let the team see the positive impact of their efforts on the overall quality of the project.
- Open communication is key: Encourage feedback, both positive and negative. Create a safe space for discussions, concerns, and ideas. When everyone feels heard, they’re more invested in finding solutions.
- Lead by example: Your actions speak louder than words. Be the first to arrive, the last to leave, and the one who always walks the talk. Your dedication to quality will inspire and motivate your team to follow suit.
Effective planning and scheduling
A well-defined plan avoids the pressure of last-minute scrambles. Each stage has its allocated time, allowing workers to focus on delivering quality over speed.
Planning helps you anticipate and allocate resources like manpower, equipment, and materials effectively. It avoids wasted time and resources, optimizing your budget and ensuring everyone has what they need to do their job well.
On the other hand, cramming tasks into tight deadlines leads to corners being cut and mistakes being made. Precise scheduling ensures each stage of the project receives the time and attention it deserves. It results in fewer errors and, ultimately, higher quality.
By anticipating risks and delays upfront, you can develop contingency plans and avoid scrambling when unforeseen issues arise. This, in turn, allows your team to focus on what matters most – building with precision, care, and excellence.
Use construction management software like PlanRadar
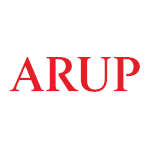
PlanRadar has enabled our site inspection teams to gather site data quickly and efficiently, whilst significantly reducing the time required to process and present this data.”
All of the steps above are simple to understand, but could be complex to undertake. But they don’t have to be. That’s where construction management software, such as PlanRadar, can help.
Our platform streamlines workflows, reduces errors, and puts real-time quality control in construction at your fingertips.
On our construction management software page has all the info you’ll need to better understand how advanced construction management software can empower your team.
Final thoughts
Improving construction project quality is a deliberate and continuous effort. It’s the choice of sturdy materials over shortcuts, the commitment to regular training over complacency, and the investment in smart tools like PlanRadar over outdated methods.
At PlanRadar, we’re passionate about empowering construction companies to build better. Our construction management software is designed to simplify your quality control processes, enhance collaboration, and provide real-time data to optimize every step of your projects.
If you’d like to see the platform in action, make sure to book a demo with one of our experts at a time and date that suits you.